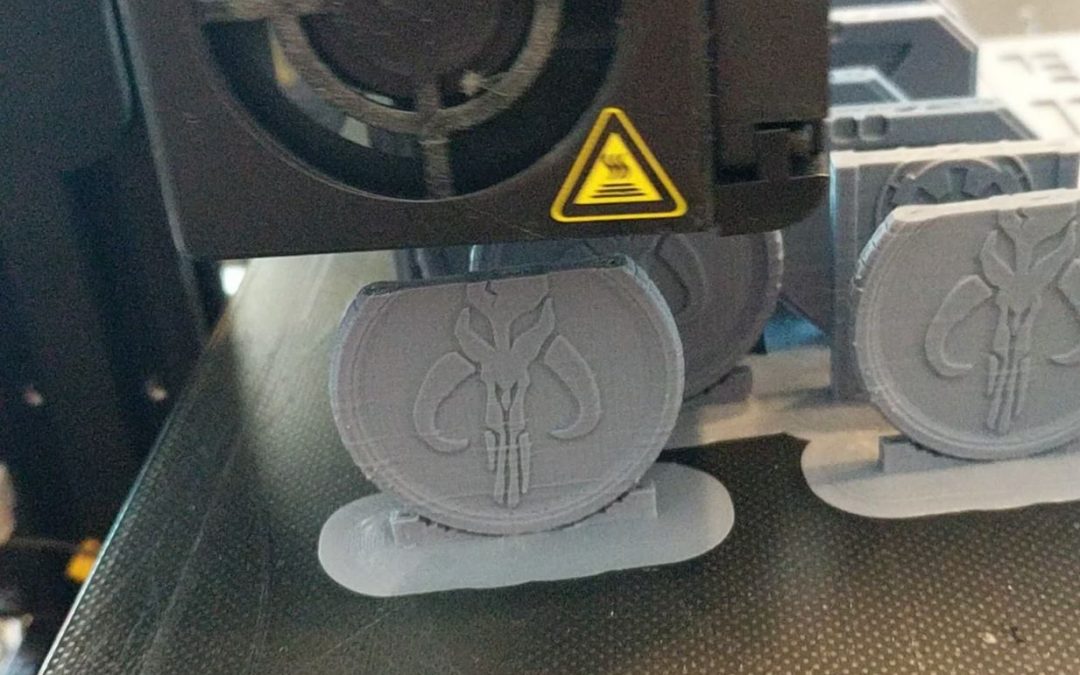
Things I Learned About My Ender 3
I’m on an Ender 3 support group on Facebook, and nearly all the comments in this group asking for help are from people who did not follow the instructions when doing the setup on their Ender 3’s in the first place. Those who are meticulous about getting the frame absolutely square and the belts as tight as they can get them without binding everything up are getting superior results.
If you’ve just bought an Ender 3, there are a few things you’ll probably want to do or try at some point.
- Make sure your frame is square. I’m serious. 90% of the problems you’re likely to have with your prints will derive from not having properly assembled the gantry.
- Make sure your bowden tube is properly trimmed (and by this I mean trimmed off exactly square) and then fully inserted into your hot end. This one error will make your life hell. If you don’t get this exactly right, you’ll get plastic plugs where your filament heats up and jams your bowden tube, requiring you to partially disassemble your hot end and possibly trim back your bowden tube to get past the clog. Having the bowden tube properly trimmed and properly inserted mostly stops this from happening. There are “fixes” to get around the clog problem, but in general they just add additional points of failure and rarely work as well as setting up your bowden tube properly in the first place.
- Replace the plastic extruder clamp with a metal one. Some printers have an extruder arm made entirely of plastic. They’re cheap, usually under $20, but the filament tends to saw through the plastic clamps over time. Sooner or later you’ll want to replace it. Newer ones have a brass liner in there that stops the filament from doing that.
- If your printer has to live inside, get a silent controller board. This makes your printer so quiet that you’ll have to do an eyeball check to see if it’s still even printing, it’s so quiet. They’re about $40. However, these silent boards can also prevent you from making linear advance calibrations that can improve the quality of your prints, so you may find yourself with a choice of quality versus machine noise while printing.
- Print a fan cowling for your CPU box to keep crap from falling into your controller box through the vent fan. Newer Ender 3’s have the vent on the bottom of the controller box, so it’s not a problem – but the older types have the slots on the top. It’s amazing how much crap can fall in there.
- Print a muffling fan cowling for your power supply box. This will drop the fan noise made by the machine by half. Be careful – doing a poor job reassembling your fan with its new housing can make it worse, not better.
- Order more bowden tube, and more nozzles, and more pneumatic clamps. These things wear out, and after about four to five months of use, they’ll start to screw up your prints. You do not want to be stuck without spare parts if you’re in the middle of a paying print job and something breaks.
- Get a glass build plate. Go to your local dollar store, and buy a cheap 9×9 square picture frame. Take the glass out of it, and throw the rest of the frame away. The picture frame glass is a quarter the weight of the official Creality glass bed and causes far fewer problems with Y-axis ringing due to its much lower inertia. Alternatively, go to IKEA and get a 1′ mirror tile, then go to your local home improvement store and get a glass cutter so you can cut the mirror tile down to the size of your printer’s bed. If you’d rather use the Creality build plate, don’t be afraid to flip it over and use the untextured side. It’ll leave a mirror-smooth bottom surface on your parts!
- Don’t use tape on your print bed. Tape is a substitute for proper bed leveling, and solves problems that haven’t existed since the introduction of heated, adjustable beds. The only time you might want to use it is if you’re using something other than PLA in your printer that sticks like mad to your printing surface, such as PETG. The tape will let you remove the part without breaking your glass.
- If you’re having particular problems getting your PLA to stick to the build plate, try a fine mist of Aquanet. It’s cheap, and compared to fiddling with the bed leveling to get it precise to the last 0.01mm, it’s a fast solution that gets you on your way and printing parts again. Some purists think this is cheating, because you can resolve sticking issues with better bed leveling, but if you have to get the parts out the door, there’s nothing wrong with doing something quick that works so you can get on with your life.
If it feels stupid, but it works, it’s not stupid. - Buy eSun PLA+ filament for printing. It runs about 10° C hotter than the usual stuff, produces much more precise, clean prints, and costs exactly the same as whatever you’re using.
- Don’t grind your filament to death. One of the things that can happen if you try to drive your printer too fast, is that you can exceed the structural integrity of the filament as it passes by the gear in your extruder. If the extruder can’t feed the filament through the print head fast enough, it’ll start digging a hole in the side of the filament at the extruder head, and then you are basically and royally screwed, and your print has failed.
- If you think vibration damping is something you need, buy a $5 yogo mat, cut it into 1 foot squares, and put a stack of four or five squares under your printer. It will kill a lot of the noise and vibration your printer makes, and may well improve the quality of your prints.
- Make sure your belts are as tight as you can get them. Don’t worry, you won’t break them. Tight belts means more precise motion and better prints.
- Experiment with printing at stupidly thin layer heights. I started experimenting with 0.08mm layer heights, and people I show the prints to, even other 3d printer owners, are amazed that these are 3d printed objects.
- Special fan housings generally do very little, and on the whole don’t improve print quality enough to bother with. Minor tweaks in your slicer settings usually have a much broader effect.
- It is possible for an Ender 3 to not want to print because it’s too cold to start with. If your printer lives in the garage or workshop, as mine does, it’s probably not in a heated environment – and that means that it can get down to under 10°C and chill your temperature sensors to the point where the printer’s firmware thinks something must be broken, and you’ll get a MINTEMP error. You could have a bad thermister, or a bad connection trace to it on the motherboard, or a bad connector, but the first thing to try is just bringing the thing inside and letting it warm up a bit. I did this and once I got the temperature of the printer up above about 8°C, the printer realized its sensors weren’t broken, and it started right up.
- Get a Raspberry Pi and load it up with a webcam and Octoprint. Being able to run your printer without having to be in the same room with it is heaven. Being able to move your printer to your garage or workshop is even better.
- Having trouble with weird surface artifacts in your prints? Slow down. This is especially true of specialty filaments like silks or silk metallics. They are extremely sensitive to print speed, and what looks like a hopeless print may come out perfectly if you cut the print speed in half.
- Have to paint your prints, but don’t like the way the parts smell afterwards? Sometimes the client wants it painted, and it’ll smell bad for quite a while once you do. White vinegar will get the smell out of the painted surfaces while not endangering the finish. Be sure to rinse off the white vinegar, or your parts will smell like vinegar instead of paint.
- Don’t bother with vibration damping feet for your printer, or special angled mounting arms for your filament spools. By in large these do nothing but waste your time and materials. (If you need to make angled printer arms so that you can fit the spool and printer into a more compact space, that’s a different problem, and you should have no qualms about doing it.)
- Octoprint suddenly won’t connect to your 3d printer? It could be the USB voltage levels. What’s happening is that it matters what order you connect your printer to your Octoprint device. If you turn on your Raspberry Pi and plug it into your printer before your printer is powered up, the motherboard in the printer will draw just enough power to make the voltage levels required to detect your printer as a USB device too low to actually do the job.
The fix is to disconnect the USB cable, power on the Octopi and the printer separately, and once you’re sure the Octopi is booted, then and only then connect the USB cable between the Pi and the Printer. Now the Pi will be able to detect the printer as a USB device, and all will be well.
Check back here periodically. I’ll be updating this list of tips as I go, and you may find out something new you didn’t know before.
-30-
Recent Comments